摘要技术柔性化成为冲压生产主流现代汽车工业具有生产规模化、车型批量小、品种变化快、多车型共线生产的特点, 车身覆盖件也随之呈现大型化、一体化的特征, 这些趋势要求冲压技术与...
技术柔性化成为冲压生产主流现代汽车工业具有生产规模化、车型批量小、品种变化快、多车型共线生产的特点, 车身覆盖件也随之呈现大型化、一体化的特征, 这些趋势要求冲压技术与设备不断向柔性化和自动化方向发展,高柔性、高效率的自动化冲压设备正在逐步取代传统的刚性生产线,成为世界冲压生产的主流。
柔性冲压设备给生产带来灵活性
冲压设备包括各种压力机、开卷、送料及校平装置等。集成化控制技术、伺服驱动技术在压力机上的应用给冲压生产带来了更多的灵活性, 大型多工位压力机、柔性冲压自动线等设备正在改写冲压生产的历史。
目前最新式的数控回转头压力机, 步冲频率可达次旧, 工件移动速度可达以上。近些年还出现了一些新的柔性冲压加工设备, 其中多点成形压力机和单点成形压力机是典型代表。多点压力机上下工作台上有许多成对布置、高度可独立控制的柱形单元, 可以完成任何三维曲面形状工件的成型。
各种曲柄压力机是应用最为广泛的冲压设备。它具有结构简单和工作效率高的优点, 但最主要的缺点之一就是缺乏“柔性” , 其滑块的运动特性曲线是固定的, 速度按正弦曲线变化, 不能调整。近些年来, 交流伺服电动机驱动技术的发展, 为解决这一问题带来了希望。日本等国已经开发了基于这一技术的机械压力机, 将运转速度任意可调的交流伺服电动机取代了速度不可调的普通感应电动机, 滑块可以实现任意的运动曲线, 实现不同的冲压工作, 例如静音冲裁、快速冲裁、分段压制及精密压等。它除了可以改善工作环境、提高工作效率、提高模具寿命及节能外, 还特别适合汽车超高强度钢板的冲压成形, 减少回弹, 提高成形精度。
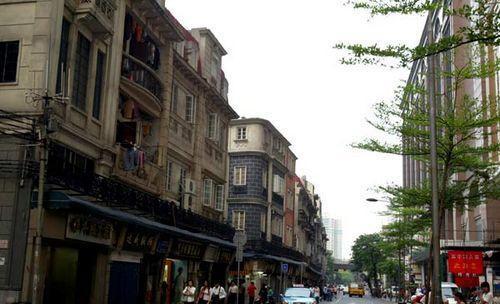
电气伺服技术:伺服系统是使物体的位置、方位、状态等输出被控量能够跟随输入目标值或给定值的任意变化的自动控制系统。
新型伺服压力机采用了适应性很强的伺服驱动技术, 将液压机的灵活性与机械压力机的高效率优点有机地结合起来, 企业可以为他们的用户提供大小批量的各种不同的冲压件, 生产能力大幅提高。日本小松公司和德国舒勒公司相继开发并已生产出了这种伺服压力机, 目前在我国国内, 一汽丰田汽车公司和广州丰田汽车公司已采用了这种设备。
伺服驱动系统最突出的特点是电动机直接与偏心曲柄齿轮相互连接, 由于电机的转速可以任意调节, 从而可以任意地调节曲柄机构的运动速度, 任意加快或减慢冲压速度。
伺服压力机的另一大特点是匹配性很高。由于伺服压力机的电机转速是可以无级调节的, 因此有可能在冲压过程中实现冲压运动和冲裁力的无级调节, 使压力机的工作曲线与各种不同的应用要求相匹配。为了保证曲柄完成精确的运动, 用户可以通过减速拉延加工实现或者保持恒定的冲压运动速度,这样不仅可以提高板材加工的质量, 而且也可延长模具的使用寿命。伺服压力机的转速变化及控制经过了合理的优化设计, 并且采用了集成化的模块, 按照模块化结构制造, 如果不需要使用其伺服功能时, 该机就可以像传统压力机一样工作, 保持恒定的功率和行程。
电气伺服技术应用最广, 主要原因是控制方便, 灵活, 容易获得驱动能源, 没有公害污染, 维护也比较容易。特别是随着电子技术和计算机软件技术的发展,它为电气伺服技术的发展提供了 广阔的前景。
大型多工位压力机在覆盖件冲压领域, 大型多工位压力机是最先进、最高效的冲压设备, 是高自动化、高柔性化的典型代表。通常由拆垛机、大型压力机、三坐标工件传送系统和码垛工位等组成。生产节拍可达一次, 是手工送料流水线的一倍, 是单机连线自动化生产线的一倍。目前世界上已能生产的大型多工位压力机。而多工位压力机的技术进步主要体现在送料技术上。送料系统越稳定, 则重复定位精度越高,其产量也就越高。因此, 亚待解决送料技术问题。
随着液压机某些关键技术的突破, 液压机在冲压方面的优势和潜能得到充分发挥, 生产率明显提高, 以及行程同步、与传送装置连锁等问题的圆满解决, 冲压生产线可以全部采用液压机, 也可以液压机与机械压力机混排使用, 但机械压力机作为主机组成的冲压生产线毕竟仍是主流。
大批量生产的汽车冲压企应为每条大型冲压自动线配置调试压 力机, 以缩短金属成型模具的试模时间, 提高大型冲压线的开动率。调试压力机主要选择液压高速试验压力机和拉伸机械压力机, 特别是在生产型机械压力机上的模具试验时间可减少, 具有巨大的应用价值。
为适应柔性化的生产要求, 压力机的所有控制功能应做到集成化, 从而实现全套模具的菜单化管理, 主要包括滑块行程调整、平衡器气压的调整、气垫行程调整以及自动化控制系统等各个环节的参数设定。具有现场通信网络、现场设备互联、互动操作性、分散功能模块、开放式功能的现场总线技术是压力机控制技术的发展方向, 对实现自动化具有明显推动作用。
目前国内生产的用于轿车大型覆盖件制造的大型冲压线已经达到了当代国际先进水平, 采用了多连杆精度优化补偿技术、联网全自动模具快速更换技术、矢量交流频调速主驱动技术及多点液压过载保护卸荷控制技术等, 应用网络技术可与生产联网, 实时监控设备状态, 具有远程通信和远程故障诊断功能, 整线支持快速送料系统, 每分钟可生产一个轿车大型覆盖件。
数控多工位压力机被誉为大型冲压设备的革命性产品, 国外发达国家各大汽车生产商。以上美国高达均采用多工位压力机 进行覆盖件的冲压生产。因该类设备技术含量高, 核心技术不为我国企业所掌握, 目前全部依赖进口,且由于其价格昂贵, 在我国的应用屈指可数。预计到年, 国内市场容量约为台套, 销售金额可达亿元, 它将具有广阔的市场前景。
提高汽车外观质量的最有效途径
在冲压生产中采用工业机器人机械手代替人工操作, 构成自动化生产单元或组成全自动生产线,是进行高速、高效、高质量的冲压生产的一种有效方法, 也是现代冲压生产技术的重要发展方向。机器人冲压生产线在国外已运用多年,但在国内很少, 特别是集合总线控制、网络数字通信等国际先进技术的全自动机器人冲压生产线在国内还没有。
柔性冲压自动线大多由一台双动拉伸压力机或多连杆单动拉伸压力机和一台单动压力机组成流水线, 生产大型车身覆盖件, 安全性高, 冲压质量好。生产线上布置自动化上下料系统, 由拆垛机、清洗涂油机、对中上料机、上下料机械手机器人、穿梭翻转传送自动输送机组成, 从毛坯的上料到冲压件下线全部自动完成。生产节拍最高为一次旧。整条冲压线长人。有些企业采用的是国际先进的高速紧凑型冲压线, 能快速提高冲压机的生产效率。板料对中采用当今先进的光学摄像系统进行定位。
拉伸压力机选用数控液压拉伸垫,先进的每个自动化单元配一个机械手, 省去了穿梭传送装置, 缩短输送距离, 减少压力机的间距, 生产节拍可达件旧。随着我国汽车市场竞争的不断加剧, 汽车的外观质量及其内在质量成为各汽车制造厂家角逐市场的先决条件已是不争的事实, 因此, 采用机械化、自动化的生产方式进行冲压生产是提高汽车外观质量的最有效的途径。
近年来, 冲压生产智能控制技术发展很快, 它在材料、工艺一体化的基础上, 依据已有材料和工艺数据库实现冲压加工过程的在线控制或智能控制他称“自适应控制” 。首先对材料或工艺参数建立在线检测系统, 当材料性能或工艺参数发生变化或产生波动时, 由自动检测系统传感器和信号转换系统在线确定相关参数的瞬时量值, 并通过计算机模拟分析和优化软件例如人工神经网络方法、专家系统确定参数变化后的最佳工艺参数组合。自动控制系统调整工艺参数后, 可以实现冲压工艺过程的自适应控制。新的生产数据逐渐积累可进一步成为后续加工过程的工艺优化基础。
自动冲压生产线的研发、冲压生产线的机械化改造、用于汽车侧围板生产的大型真空上料冲压机床的制造促进了汽车工业的飞速发展。对于国内汽车冲压件生产企业来说, 最有价值的技术提升集中表现在冲压件的自动化运输、自动化传递装置上以及在冲压设备上料自动化和以产品为导向的冲压生产过程中。由于在变形加工过程中液压技术的极限不易突破, 因此只能向机械自动化要效益, 而且不能仅仅在冲压工艺过程中向机械自动化要效益, 应当也向冲压工艺技术以外的领域要效益、向新的冲压件传送方式、向冲压件下线方式要效益,向所有能获得经济效益的领域索取效益。新型的集成式快速传送系统可为压力机与压力机之间直接传送, 生产节拍可达一次旧。
机械手臂末端可自动编程进行角度调整, 以适应模具的型槽位置。在大型及特大型冲压件的生产过程中, 坚固有力的冲压件传送机构不仅可在大型工件冲压和双件冲压一次冲压两个成品的生产过程中得到广泛的应用, 而且也可以在汽车零部件生产过程中广泛应用。摆臂式冲压件传送系统将会给冲压设备在快速更换模具方面以极大的支持和帮助, 它实现了冲压模具和工件的同时输出, 从而为实现多功能的冲压生产线奠定了基础。
汽车冲压件加工工艺技术变革
在世界汽车产品变化多样的时代, 模具多样化和模具更换周期短的特点变得尤为突出, 同时对冲压工艺技术提出了新的要求,带来了汽车冲压件生产加工工艺技术的变革。
汽车冲压件具有良好的工艺性和经济性, 衡量其水平的重要标志有冲压件的工序数、车身总成的分块数量和尺寸大小、冲压件的结构等因素。减少冲压过程的工序数意味着减少冲压件数、节省工装数量、简化冲压过程的传送装置、缩减操作人员和设备占地面积等, 是节约投资及能耗的极佳措施, 所以冲压制造商都能把冲压工序数设计作为降低汽车制造成本的重要途径, 甚至不惜改进产品设计来满足制造工艺的要求, 同时还采用尽量大尺寸的合理的车身总成分块, 如整块式车身左右侧板及车顶盖板,既可使汽车外形更加美观实用, 减少空气阻力, 又可减少冲压件数量及焊点, 能有效地降低成本。
在制定工件的冲压工艺时, 处理工序的分散与集中是比较复杂的问题。它取决于工件的批量、结构形状、质量要求、工艺特点等。对于通常是大批量生产的汽车冲压件, 应当尽量采取工序集中的方案, 采用复合或级进模进行冲压,这样既提高生产率, 又能做到安全生产。实践经验表明, 对于复合模, 集中到一副模具上的工序数量不宜太多, 一般为一个工序,最多个, 对于级进模, 集中的工序数可以多一些, 因为其模具结构的布局范围自由度更大。
随着中高级轿车车身整体侧围冲压技术的推广以及压力机台面的增大, 冲压工艺也得到了快速发展, 车门、翼子板等冲压件从过去的一模单件发展为双槽模生产, 生产效率成倍提高, 最新已发展到车门内外板采用四型槽冲模生产, 生产效率又翻了一番。产量较大时,采用多件同时冲压, 可使模具费、材料费和加工费都得到降低, 对成形工艺来说, 也有利于材料应力、应变对称均匀, 还提高了生产效率, 降低了能源消耗。双件生产的最新发展趋势是内外板同时生产,其优点是生产数量匹配, 还可同时送焊装线及时压合, 物流顺畅、便捷。
“ 上海市模协” 征稿
上海市模具技术协会微信公众号“ 上海市模协”跨入八个年头,为模具及相关领域的发展作出重要贡献。当前疫情肆虐,我们将继续与您密切联系和同舟共济。我们欢迎
您一如既往为“ 上海市模协”投稿,内容: 模具及相关领域的动态、前沿技术、科研成果、企业管理等等文章,让模具及相关领域的同仁们与您分享。
投稿联系人:董先生
邮箱:
[email protected]
上海市模具技术协会
地址:上海市黄浦区制造局路787号301~303室
电邮:
[email protected]
网址:www.shmould.org
更多资讯请关注